Warehouses, whether they house mattresses, furniture or fruit baskets, do have a lot of similarities; but I can tell you that storing mattresses has enough of its own peculiarities to warrant a special discussion. If you’ve ever managed a mattress warehouse, you’ll know what I’m talking about. In this issue we will cover information for ongoing operations, but if you haven’t set up a mattress warehouse before, are looking for new/additional space, or want a quick review of important considerations you may want to check out the first part of this article posted to Furniture World Magazine’s website (
Better Bedding and Mattress Sales Series) that includes the following information:
- Site Selection/ Location.
- Desirable mattress warehouse features.
- Rules of thumb for choosing the right warehouse size.
- Special features you should look for.
- Security of the warehouselocation.
- Specific qualities to look for when hiring warehouse personnel.
- Theft prevention against internal land external threats.
Over the years, occasionally a common sense idea will occur to the store owner/warehouse manager about how to arrange a mattress warehouse for optimum efficiency. Here is a collection of those ideas that have occurred to me. While I’m sure that many owners are familiar with these common sense principles, this article can be useful as a checklist when opening a new warehouse or when preparing a training guide for new warehouse personnel.
We’ll start with where to put the mattresses.
Most warehouses found in the United States have to be operated under prevailing safety codes and laws. This starts with the usual fact that your space almost always has a front door where you walk in, an overhead loading door where all inventory comes in and goes out again, and a back door, which is required by virtually all fire prevention codes. When arranging your warehouse, make sure you do not block the back door. This sounds only too obvious, but many times I have seen careless employees stack frames, returns, etc. against the back door. Why do they do this? Because most warehouses are cramped for space, they are scurrying around looking for some open spot to drop something, and lo and behold, there is space discovered in the little corridor that leads to the back door. The Fire Marshal, who will make occasional visits, does not like this. He will write you up, and he will make visits more often because he now thinks you may be a serial violator of this important fire code. Another problem with back doors is that merchandise has a funny way of finding its way out of them when no one is looking. Back doors are also a good funnel thru which unwanted or discarded items, such as pallets, old mattresses that were picked up, broken frames, etc., can be disposed. The back side of many warehouses looks like a bombed out city dump. So, the back door, while a necessary feature, possess some special problems.
Where and how do you place your mattresses? I strongly recommend, before occupying new space, that you get an accurate layout of the premises, with correct dimensions. Then design a floor plan of how you want the place to look. In a bigger warehouse, there can be quite a distance between the back and the loading dock. For that reason, try to place heavier mattresses, such as kings (especially memory foam) toward the front of the building. Best selling models should probably be placed closer to the front of the warehouse. These are just ideas to make things a little easier and more efficient. Don’t forget, in your design, to leave plenty of space in your “staging area” for unloading trucks. The size of the deliveries should dictate how much space you need.
When designing your layout, always remember aisle width. The aisles between your mattress stacks must be wide enough to comfortably have room to remove mattresses and foundations from your stacks to get to the desired pieces. The piece or pieces you want will often (or in the case of our stores, always) be at the bottom of an 8 to 10 piece-high stack. Leave enough space to get out the top pieces easily, remove the ones you want, and then put the stack back the way it was.
Unlike furniture, a pallet jack or fork lift is rarely ever used with mattresses. Therefore, I never found it useful to make the aisles wide enough to accommodate one of those monsters. I like my aisles just barely wide enough to do the work at hand. Too wide and you waste expensive and valuable space.
I recommend keeping frame storage close to the front door. Frames are an incidental but necessary item, and probably 75 percent of mattress sales tickets include frames. So, don’t waste time and effort running to the back of your warehouse every time you need a frame, which is probably several times a day.
Mattress Storage
The first rule in storing mattresses, assuming of course, you have an airtight, water proof, clean and dust-free space, is to STACK your mattresses on top of each other. Do not store your mattresses on their sides, or borders. They may be easier to retrieve that way, but gravity, (which is not only a good idea, but also the law) will not be denied. Padding will shift if mattresses are stacked on their side, and that is not a good thing.
How high should you stack your mattresses? Our simple rule was to limit the height of the stack to “no higher than the shortest warehouse person can easily reach.” Let’s say that you get a big load in on Thursday, and your 6’6” warehouse guy unloads and stacks everything. But he’s off on Friday, and the 5’7” guy is working. He may have a hard time getting that top mattress off the stack, right? He will eventually get it down, of course, but how much valuable time will he waste figuring this out?
Here are more mattress stacking rules to think about.
- The bottom 3 or 4 (or 5) pieces should be foundations. Why? To stabilize your stack. Mattresses placed on the bottom of an 8 piece high stack become pretty wobbly.
- Never allow the bottom of a foundation, where the dust cover and staples are, to come in contact with a mattress. To do this is just begging for snagged, ripped or torn mattress covers.
- This next rule is such a common sense idea, that it is hard to believe it is so widely violated. Stack same sizes in the same stacks. Don’t stack fulls in the same stacks as queens.
- ALWAYS stack mattresses with the labels OUT, where they can be read easily by warehouse people or inventory takers. If your mattresses are not clearly labeled by the manufacturer, make up your own labels and affix them to the mattress after the truck is unloaded and before they go in the stack.
- Try to place matching pieces (mattresses and foundations) in the same stack, so that you don’t have to dig through more than one stack to retrieve your desired pieces. With today’s universal foundations, this is much easier than it used to be.
Handling Mattresses
Since we’re on the subject of storing mattresses, let’s talk a little bit about how to properly handle mattresses and foundations. First, let me start by saying that every warehouse person should be trained, from day one as an employee, on how to handle mattresses and on the importance of never violating the warehouse rules.
- Mattresses should not be carried using the crimped up bag as a handle. Most are handled this way, but doing so frequently tears or rips the bag. More on this problem later. They should also not be carried by the handles (if they are present).
- Most strong young men can carry a queen size alone, and some can probably carry a king size. Just because they can doesn’t mean they should. There will be fewer problems if all queen and kings are handled by two people, one on each end (actually lifting the mattress without using the bag as a makeshift handle.) If, however, one is all you have, the mattress can be carried one of two ways. If the carrier is tall enough, the mattress (queen and smaller) can be carried under the arm (as long as the carrier is careful not to drag the mattress.) The other way is to stand the mattress up, lean it at a 45 degree angle, grasp the lower side by the border wire edge (this is harder to do with foam encased models), bend the knees and lift the mattress on the shoulder and carry.
- Never drag or push a mattress. This important rule was my first instruction to new-hires. Violation of this rule would result in immediate termination of employment. Why? You don’t have to drag a mattress very far across a rough concrete floor (the surface of most warehouse floors) to burn through the plastic and into the fabric. “Burned” mattresses lose value in a hurry. I reminded warehouse staff that one burned premium mattress cost more than a full week of their salary.
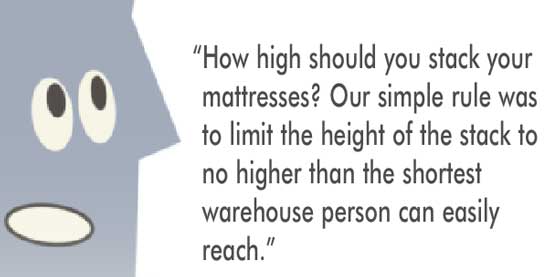
Some Miscellaneous Mattress Warehouse Policies
- Off-Loading: We talked about having a staging area to place mattresses as a truck is being unloaded. This is one occasion when it is permissible to lean mattresses rather than to stack them. You should have an off-loading procedure which allows for easy check-off against the packing slip. Note: the warehouse supervisor, or off-loader, should obtain his copy of the packing slip before any piece comes off the truck. Efficiency and speed in off-loading and check-off is more important now than ever because of new trucking regulations. (See Furniture World, Magazine September/ October 2013, “New Trucking Regs, by Dan Bolger at www.furninfo.com/Authors/Dan%20Bolger/2). So, do your shipper a favor; be ready when the truck arrives.
- Staging: This should be obvious, but I’ll mention it anyway. Don’t integrate newly off-loaded merchandise into your warehouse stacks until it has been checked off and signed off by the shipper’s delivery driver. Leave it in the staging area until it has been signed off.
- Paperwork: The person checking off the pieces against the packing slip must note any discrepancies, such as missing pieces, wrong pieces (size or model of mattress). These errors must be listed on the shipper’s manifest and brought to the driver’s attention. The driver must sign both his copy and the store’s copy showing his agreement that there were, indeed, errors. Make sure that the store gets a signed copy for its records.
- Pulling Mattresses: Here is a cautionary note on pulling mattresses and foundations out of stacks. Hurried (and harried) warehouse men will frequently try to shortcut the annoying problem of removing a piece that is 6 layers down in the stack. This shortcut is to try to pull out the “buried” piece without removing the pieces on top (the “overburden.”) Don’t do this. Pulling a mattress with 500 pounds of other mattresses stacked on top cannot possibly do anybody or anything any good. Take the time to remove the overburden before pulling the desired piece.
- Torn bags: Pieces that are lifted by using a crimped bag as a handle will invariably result in torn bags. When bags get torn, it is important to repair the tear quickly. A tear in the bag allows in dust and dirt. Mattresses in stacks get moved a lot, and the mattress with the torn bag will sometimes have the exposed mattress fabric directly in contact with the floor. Use clear packing tape to overlap seams and tape the damaged bag.
- Re-bagging your floor models: Should you buy new bags to re-bag floor models when they are sold off? Probably, but it is tempting, and less expensive, to save old bags for re-bagging. When re-bagging, be careful to bag up the floor model in the same bag from which it was removed. And, make sure it is thoroughly taped to prevent dust and dirt contamination.
- Load-outs: Make sure that all warehouse personnel know how to safely and properly load a customer’s vehicle. I could write a separate article on the points and hazards of doing load-outs, but I’ll try to be brief. Most store policies on load-outs usually follow one or the other of two possible philosophies. To tie down or not to tie down. Some stores believe that it is a liability hazard to tie down (secure to the vehicle) a customer’s merchandise, and insist that the customer secure his own merchandise. Other stores follow the sensible idea that most customers do not know how to properly secure merchandise to their vehicle. Thus the store’s unwillingness to secure the customer’s merchandise represents a far greater liability hazard than letting the customer fumble around with it. Which is more legally correct? I don’t know. Ask your insurance provider. Maybe they have an answer.
If your store policy is to secure the customer’s merchandise, then you must provide strong twine, or rope and train all personnel how to tie the right kind of knots to safely bind the merchandise to the vehicle. Warehouse personnel should also be taught the proper location on the vehicle to use as tie and secure points. Don’t damage the paint on the customer’s brand new pick-up. After the tie-down is completed, ask the customer if he is satisfied with it, and if he is confident that his merchandise will still be on his vehicle when he pulls into his driveway.
What if your customer wants to pick up a king size mattress and pulls up to your warehouse door driving an old Volkswagen bug? I’ve actually had this happen. The customer must be advised of the problem, if not already aware of it. If the customer insists that you proceed with the load-out (which mine did), then you must ask the customer to sign a form waiving you and the store from any responsibility if any problem should occur. (Check with your legal counsel on this. Don’t take my word for it.)
- Liability hazards: The warehouse is loaded with them. It is for this reason that it makes good sense to prohibit non-employees from entering the warehouse. Of course, in a small town where people are friendly and helpful, and only one guy is available to load a heavy king, this rule may have to be suspended for the moment.
- Deliveries: I know that deliveries are part of warehouse management, but there are so many facets to delivery, that I will save that subject for another time and place.
- Walking the warehouse: I know that busy store owners sometimes get somewhat relaxed about the warehouse. Things seem to be running smoothly. It is not a good idea to get too comfortable with this idea. Owners and managers should do a thorough walk-thru at least weekly and keep an eye out for the above items. This walk-thru is separate and apart from the regular monthly inventory that should be routine.
To repeat one final point, never forget, your warehouse is an extension of your store. If you believe the old adage, “A chain is only as strong as its weakest link” then never let your warehouse become that weak link.