Unusual circumstances called for a creative solution when Grace Furniture found a need to expand and upgrade their warehouse facilities.
Grace Furniture, owned andmanaged by second and third generation family members, was founded by Frank Grace of Marcy New York in 1940. The store is a full line furniture and accessory destination point featuring medium to high-end lines such as Harden, Hancock & Moore, Durham, Stanley, Sumter, Hooker, Wesley Hall, Hallagan, Stearns & Foster and Sealy. There is clearly a focus on providing excellent designer assistance to their clientele. Over 90% of sales are special order to customers within 75 miles, delivered by their own warehouse/delivery crews in two trucks and a van.
Recognizing that keeping current on furniture retailing practices was essential, John Grace participated in the 1997 NHFA Management Development Institute program in Dallas Texas. He came home armed with goals to make major improvements to the back-end of the business, particularly the warehouse and prep operations. Their existing 6,000 foot warehouse had a 12 foot ceiling height, one receiving door, one shipping door and attic space. This space, plus supplemental warehouse space at their original store, was inadequate to support their 25,000 foot showroom and future plans.
There were lots of things John and his Dad Bill wanted to do, but available resources limited how much could be done at any given time. Regardless, they had a plan that they implemented step by step. First they tackled the basics of inventory management and improved practices while struggling with the facilities issue. In 1999 they decided on a plan to build a 10,000 square foot warehouse with a 28 foot ceiling height to be built at the store’s rear to replace the existing warehouse. The planned effective cube would triple their capacity. The clear advantages of an on site warehouse were convenience for access, more effective management oversight and lower overhead costs (they already owned the land on which the facility was to be built).
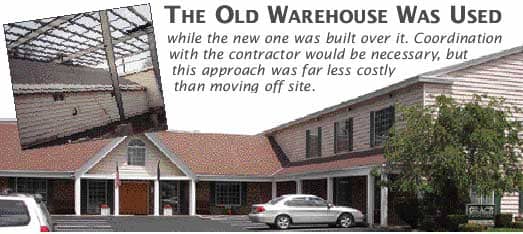
The new warehouse structure was to be a basic Butler pre-engineered frame with the exterior dressed up to compliment the store and surrounding neighborhood. Convenient and economical temporary outside warehouse space wasn’t available for the six to eight month construction period, so an outside-the-box solution was created. They kept using the existing warehouse while the new warehouse was built over it. Coordination with the contractor was necessary, but this approach was far less costly than moving off site.
Foundations were laid outside the existing building in September 2000 and the shell was essentially completed in November. At that point, a temporary wall was erected and the operation shifted to the back half of the new warehouse. The old warehouse was demolished and the front half completed over the harsh upstate New York winter. During the entire process, Grace Furniture never missed a shipping day related to warehouse construction issues. This entire warehouse was completed by May 2001 and available for floor storage.
The final phase of adding racks and a picker was completed in late 2003. That busy year, Grace Furniture was also selected “Retailer of the Year” by the Empire State Home Furnishings Representatives Association. The Association is comprised of 95 members and covers upstate New York furniture stores. The award is given annually to a retailer in the state for creating mutually successful partnerships with representatives and vendors and exemplifying professionalism in furniture retailing.
Bill Grace commented “The new facility has made a world of difference. We have sufficient space to properly prep every piece and excellent ambient lighting that assures our quality. Customer satisfaction is greatly improved and we can take a customer into the warehouse knowing that it is always presentable.” His son John likes the fact that when furniture comes in, it is put in the racks where it stays until the balance of the order comes in or the customer is ready for delivery. There is no damage and employee productivity is great. It also has adequate space for an annual warehouse fall theme sale. The next project on their list is transitioning to bar coding.
Looking back, John reflects that it was a challenge to accomplish the plan, but the end results have exceeded their expectations. I commend them for looking far enough into the future and having the tenacity to follow the plan at a pace they could manage effectively. Their project certainly confirms my long standing statement... “There isn’t a cookie cutter solution for furniture retailer warehouses.”
Contributing editor Dan Bolger of The Bolger Group helps companies achieve improved transportation, warehousing and logistics. You can send inquiries on any aspect of this article or on transportation, warehousing or logistics issues to Dan at dbolger@furninfo.com.